Understanding the Manual Handling Hazards
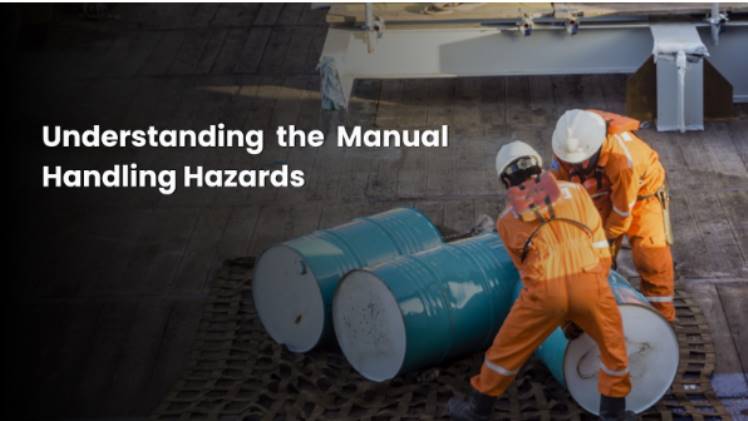
Few challenges are as widespread in the workplace as manual handling dangers. Thousands of employees are injured yearly while lifting, carrying, pushing, or hauling big goods, resulting in physical pain, lost productivity, and significant financial costs for organisations. However, these dangers may be considerably decreased with good training and the adoption of effective techniques. This blog discusses critical tactics for reducing Manual Handling Hazards, emphasising the value of Manual Handling Certification in promoting safety.
Table of contents
- The Role of Manual Handling Certification
- Anatomy and Physiology
- Risk Assessment
- Proper Techniques
- Equipment Usage
- Emergency Procedures
- Legal Obligations
- Implementing Effective Strategies
- Task Assessment and Redesign
- Training and Awareness Programs
- Mechanical Aids and Equipment
- Establishing Clear Guidelines
- Employee Involvement
- Regular Health Checks
- Reporting and Investigation
- Ergonomic Workspace Design
- Encouraging Breaks and Rotation
- Regular Review and Adaptation
- Conclusion
The Role of Manual Handling Certification
Manual Handling Certification programmes are intended to provide employees with the information and abilities required to safely and effectively conduct manual handling jobs. One of the most effective measures for reducing manual handling hazards is ensuring that personnel obtain sufficient training and certification.
These certification programmes cover a variety of subjects, including:
Anatomy and Physiology
Understanding how the human body operates and how different manual handling duties influence it is critical to avoiding accidents. Manual Handling Certification programmes teach students about the musculoskeletal system and its weaknesses.
Risk Assessment
The first step in preventing manual handling dangers is to identify them. Certification programmes educate people on identifying the risks associated with certain jobs and how to implement control mechanisms to reduce those risks.
Proper Techniques
Manual handling certification is focused on learning proper lifting, carrying, and pushing/pulling skills. Employees are taught to utilise their body’s strength more effectively, decreasing pressure on muscles and joints.
Equipment Usage
Equipment such as trolleys, hoists, and forklifts are often used in manual handling. Certification programmes educate participants on how to operate such devices safely.
Emergency Procedures
Knowing how to react quickly and efficiently in an accident or injury is critical. Manual handling certification covers first aid and emergency procedures training.
Legal Obligations
Employers are legally compelled to create a safe working environment. Participants in certification classes learn about their rights and responsibilities in this area.
Organisations that invest in Manual Handling Certification for their staff display a commitment to safety and lower the chance of workplace injuries and the expenses connected with them.
Implementing Effective Strategies
Aside from certification, organisations may take the following techniques to reduce manual handling risks:
Task Assessment and Redesign
Begin by examining your organisation’s manual handling duties. Determine if high-risk tasks may be altered to lessen physical strain on staff. This might include using mechanical assistance or changing the arrangement of workstations.
Training and Awareness Programs
Employees must be updated on best practices and safety procedures via ongoing training and awareness programmes. Refresher training regularly might assist in reinforcing correct manual handling methods and avoid complacency.
Mechanical Aids and Equipment
Invest in mechanical aids and equipment to help staff with manual handling duties. Forklifts, conveyor belts, and lifting devices are examples of such equipment. Ensure that these tools are well-maintained and are regularly examined for safety.
Establish Clear Guidelines
Create and explain explicit manual handling work rules. These policies should contain detailed guidance on how to do activities safely and effectively. Encourage staff to strictly adhere to these requirements.
Employee Involvement
Employees should be involved in the identification and resolution of manual handling risks. Front-line workers often provide useful insights into possible problems and may help the development of effective solutions.
Regular Health Checks
Implement frequent health tests to assess the physical well-being of manual handling staff. Early identification of musculoskeletal problems allows for prompt management and prevention.
Reporting and Investigation
Create a mechanism for reporting and investigating manual handling events or near-misses. Analysing these instances may aid in the identification of patterns and opportunities for improvement.
Ergonomic Workspace Design
Workspaces should be designed with ergonomics in mind. Workstations should be adaptable to suit various body shapes and to encourage healthy posture. Where required, provide supportive seats and anti-fatigue mats.
Encourage Breaks and Rotation
To decrease weariness, encourage staff to take frequent breaks. Implement job rotation to save employees from overworking themselves by repeating the same manual handling duties repeatedly.
Review and Adapt
Finally, examine and update your manual handling safety methods regularly. New dangers may develop when workplace dynamics change, and previous remedies become less effective. Continue to be proactive in resolving these issues.
Conclusion
Manual Handling Certification is critical in ensuring staff have the skills and knowledge to execute their duties safely. It should, however, be just one component of a complete safety programme that includes continuing training, equipment maintenance, and a dedication to continual development. Organisations may protect their workers from manual handling risks, prevent injuries, and create a safer and more productive work environment by prioritising safety and adopting these successful techniques.